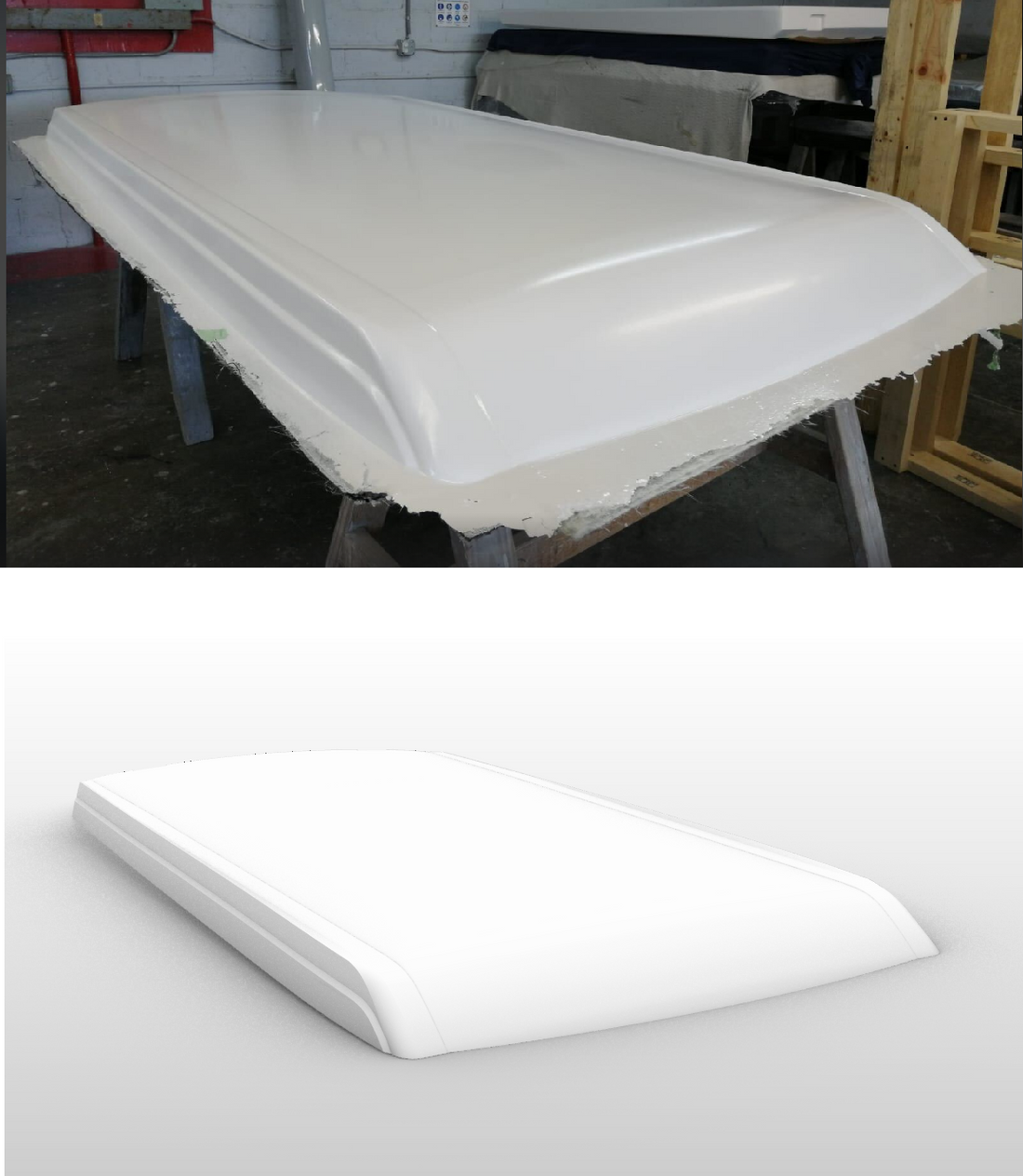
Bronco Pop-Top Prototype Top out of the mold
Share
Concept to CAD to an actual part…long time coming, too long...
Building a new composite (Fiberglass) camper starts with a set of hard dimensions based on the vehicle it will fit. Once we have those from both 3D scans and data from the manufacturer if available (thanks Ford!) the fit begins.
Cars are a balance of form and function. The challenge is always to make the camper part of the vehicle, so it looks intentional, original and functional. With modern CAD, the design can be rendered, rotated, scaled and viewed in perspective but in the end, it's only when the actual part is mounted that the "looks right" test is passed.
To do that test, we start with a soft tool. The idea is that before building the hard tool to be used for production, we use a temporary tool to create a physical part to set on the vehicle. We check the visual fit, but also aim to find areas where we may see issues in production such as cut lines, or areas that are hard to mold. We can also check the shrink of the part.
Unlike metal, composites shrink in production so the design is scaled to allow for that. The amount of shrink is estimated based on the resin and materials in the part, but the final test is to make the part and see if it hit the calculations, as sometimes internal stresses during curing can warp or move the part.
With that review is complete, we make any changes, which are usually minor, and then proceed to finishing a production tool. It is really vital to get hard tool perfect, as it will be used for a long time. (As an example, we are still using the original hard tool for our ECamper from 2007!)